POWERTRANS, La maintenance comme levier de l’excellence opérationnelle
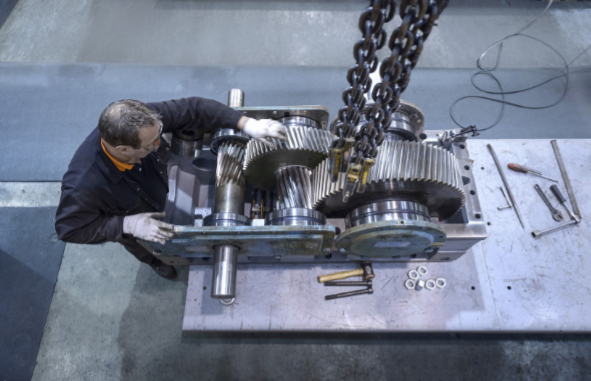
Une maintenance réfléchie au service de la productivité
Réparer, entretenir, prévenir, maintenir, voilà ce que nous dicte le bon sens face à l’entretien de machines industrielles lourdes et couteuses. Mais il y a de grandes nuances dans la façon de procéder des entreprises. Petit glossaire pour aider notre compréhension de ce secteur : la maintenance curative ou corrective consiste à réparer ou remplacer l’élément défectueux ; la maintenance préventive vise à prévenir, comme son nom l’indique, les dysfonctionnements par des entretiens réguliers et enfin la maintenance prédictive permet une surveillance constante des équipements pour une analyse précise du comportement des outils et leur évolution dans le temps. Faisons le point avec Christian SCHNEIDER, dirigeant de la société POWERTRANS, spécialiste de la transmission et régulation de vitesse, qui a développé depuis 2018 un pôle maintenance.
Le développement de la maintenance prédictive s’est accéléré depuis 2020, mais ce n’est finalement qu’un retour au bon sens de nos anciens. »« La maintenance ce n’est pas simplement réparer, c’est avant tout expertiser.
Maintenance » peut-elle vraiment rimer avec « Performance » industrielle ?
La maintenance est un poste crucial des entreprises industrielles, quel que soit leur secteur d’activité. Une machine à l’arrêt ou qui fonctionne mal, c’est une production amputée et par conséquent des ventes perdues, les répercussions peuvent être catastrophiques. Chez POWERTRANS, notre savoir-faire nous permet de faire, depuis de nombreuses années, de la maintenance curative mais nous encourageons nos clients à la mise en place d’une véritable stratégie de maintenance prévisionnelle. Le but étant d’optimiser la valeur de leurs actifs tout au long de leur cycle de vie et voire plus. Le développement de la maintenance prédictive s’est accéléré depuis 2020, mais ce n’est finalement qu’un retour au bon sens de nos anciens, nous devons penser long terme plutôt que court terme, arrêter de jeter ou de remplacer sans savoir d’où vient le problème, entretenir et surtout opter pour une approche globale.
Comment ça marche ?
Nous réalisons des études et des analyses très poussées, les données recueillies sont exploitées pour anticiper l’évolution et les réactions des machines, non seulement pour réduire la fréquence des pannes mais également pour en optimiser l’utilisation. C’est certes une maintenance plus coûteuse et complexe à mettre en place, cela dit les bénéfices en sont également plus grands à long terme.
Concrètement, comment cela se traduit ?
Prenons l’exemple d’une usine agro-alimentaire dont un réducteur inox était régulièrement changé car l’arbre grande vitesse était soumis à une torsion sous l’action du moteur. Après analyse du contexte et du fonctionnement, nous avons remplacé l’arbre inox en question par un en acier bien plus résistant et totalement adapté à l’utilisation alimentaire dans ce cas précis. Autre exemple dans une usine d’étirage de film plastique qui changeait tous les 2 ans un de ses plus gros réducteurs, dentelure usée, butée cassée, sans avoir d’explications. Le démontage nous a permis de mettre en exergue un problème d’échauffement dû à un mauvais circuit de l’huile dans le réducteur. Un changement de tringlerie pour une meilleure circulation des fluides a résolu le problème et le réducteur va bientôt fêter ses 3 ans de bon fonctionnement. La maintenance ce n’est pas simplement réparer, c’est avant tout expertiser. Nous créons un véritable partenariat avec nos clients pour analyser leur fonctionnement, prévenir le vieillissement des machines et adapter nos réponses. Nous avons réalisé de lourds investissements en matériels et en structure pour développer cette activité. nous devenons leur service de maintenance externalisé et l’engagement qui nous lie garanti une protection maximale à nos clients.
En parallèle, notre activité principale de distribution industrielle de matériel de transmission nous permet de proposer si la réparation n’est pas possible, une gamme complète de tambours moteurs réparables, réducteurs, vérins…
A côté de la gamme standard, nous proposons des produits spécifiques sur mesure.
De part sa conception, le tambour moteur consomme moins d’énergie (efficacité mécanique réduit les coûts d’énergie) et son entretien se fait après 50000 heures de fonctionnement. (Quasi-absence d’entretien réduit les coûts d’exploitation)